Tap Nomenclature
Tapping is one of the most difficult machining operations for a number of reasons. It is the only tool that is required to stop its rotation, feed and cutting action, then reverse itself out of the workpiece. This action places tremendous torque on the tool. Additionally, the relationship between the feed and speed is fixed and cannot be changed independently of each other. Similar to a drill, a tap must also remove the excess material removed from the workpiece (chips), while allowing cutting fluid to the cutting edge.
What is a Cutting Tap?
A cutting tap is a cylindrical rotary cutting tool having multiple cutting teeth to create an internal helical groove (screw thread) in a workpiece and two or more straight or spiral flutes to allow for the removal of chips and the passage of cutting fluid to lubricate and cool the cutting edges. It also could be described as a multi-tooth, single point, rotary cutting tool. That description is accurate for the cutting action as the teeth on the tool are independent of each other and each tooth progressively cuts a portion of the helical groove (screw thread) until the full required depth has been reached.
Looking at a tap along the longitudinal axis, the tap consists of three major parts.
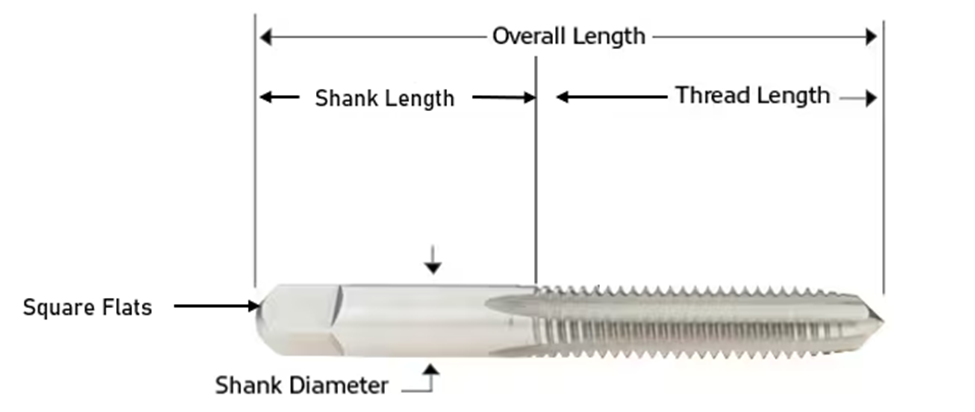
- The square or flats of the tap.
- The shank of the tap.
- The threaded area or body of the tap.
The square of the tap is used to provide a secure process to firmly hold the tap and absorb the torque so that it may be rotated to perform the cutting action.
The shank allows for clearance from the tap holder so the chips can clear the part and coolant can access the workpiece. A portion of the shank also fits in the toolholder to stabilize the tool to eliminate deviation.
The threaded portion creates the helical groove or screw thread. The nose of the tap consists of the point diameter and chamfer. The smallest part (minimum diameter) of the point diameter is smaller than the smallest recommended hole size prior to tapping. This allows the tap to enter the hole under all circumstances to cut the screw thread.
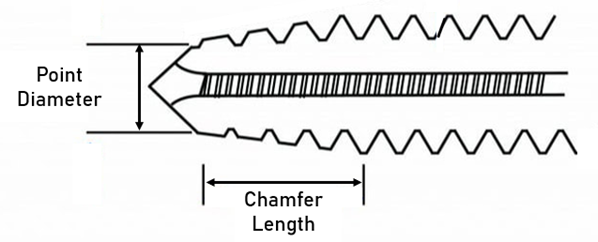
The chamfer is the portion of the tap that actually performs the cutting action. The remainder of the threaded area simply follows the helical groove and helps stabilize the tap. Often this remainder of the threaded area may have a small “back taper” that helps reduce rubbing and friction, reducing heat buildup.
The flutes are the area removed from the body of the tap allowing clearance for chips to be removed and for cutting fluid to reach the cutting edges. The remaining area where the actual threads are cut is called the land.
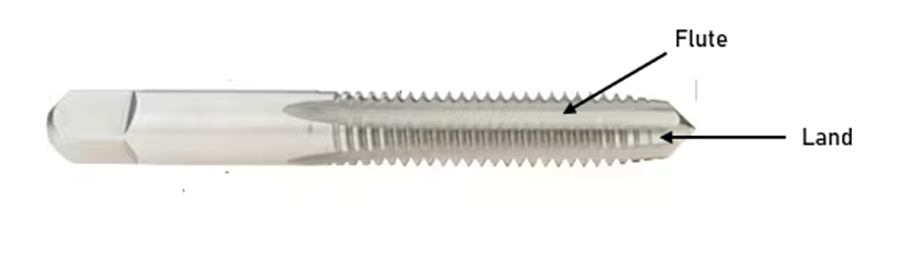